
Titan-Jan
Fa. Dosengitarre
Hallo zusammen 
Nach schier endloser Hausbau- und Werkstatteinrichtphase geht's nun endlich wieder richtig in Richtung Gitarrenbau bei mir
Ich möchte eine Reisegitarre bauen - möglichst klein und leicht aber mit voller Mensur, headless mit einer Tuning-Bridge. Nach ein bisschen Recherche hat mir vor allem die "Spirit" von Steinberger sehr gut gefallen. Die Form ist einfach auf's absolut notwendigste reduziert und gefällt mir trotzdem: https://www.thomann.de/de/steinberger_g ... 8077684508
Nun brauche ich kein Tremolo, dafür wollte ich aber ein wenig "Offset" in die Kontur reinbringen und Fächerbunde integrieren. Single Bridges zu kaufen ist mir ehrlich gesagt zu teuer. Deswegen werde ich sie selbst konstruieren, das ist aber nochmal ein anderes Thema, das erläutere ich nochmal ausführlich in einem späteren Post.
Außerdem sollen Noname-Telecaster PUs rein, die ich noch übrig habe. Im Grunde habe ich also schon alles da, nur Trussrod und Gurtpins musste ich kaufen - und eben dann die Teile für Tuner und Klemmsattel.
Das ist nun der Stand im CAD:
Es stecken also schon etliche Planungsstunden drin... aber mit diesem Startpost mache ich mir selber ein bisschen Druck, damit es nicht beim Planen bleibt, sondern auch in die Umsetzung kommt
Viel Spaß beim Zugucken und munteren kommentieren!
Nach schier endloser Hausbau- und Werkstatteinrichtphase geht's nun endlich wieder richtig in Richtung Gitarrenbau bei mir
Ich möchte eine Reisegitarre bauen - möglichst klein und leicht aber mit voller Mensur, headless mit einer Tuning-Bridge. Nach ein bisschen Recherche hat mir vor allem die "Spirit" von Steinberger sehr gut gefallen. Die Form ist einfach auf's absolut notwendigste reduziert und gefällt mir trotzdem: https://www.thomann.de/de/steinberger_g ... 8077684508
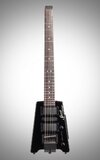
Nun brauche ich kein Tremolo, dafür wollte ich aber ein wenig "Offset" in die Kontur reinbringen und Fächerbunde integrieren. Single Bridges zu kaufen ist mir ehrlich gesagt zu teuer. Deswegen werde ich sie selbst konstruieren, das ist aber nochmal ein anderes Thema, das erläutere ich nochmal ausführlich in einem späteren Post.
Außerdem sollen Noname-Telecaster PUs rein, die ich noch übrig habe. Im Grunde habe ich also schon alles da, nur Trussrod und Gurtpins musste ich kaufen - und eben dann die Teile für Tuner und Klemmsattel.
Das ist nun der Stand im CAD:
Es stecken also schon etliche Planungsstunden drin... aber mit diesem Startpost mache ich mir selber ein bisschen Druck, damit es nicht beim Planen bleibt, sondern auch in die Umsetzung kommt

Viel Spaß beim Zugucken und munteren kommentieren!
- Eigenschaft